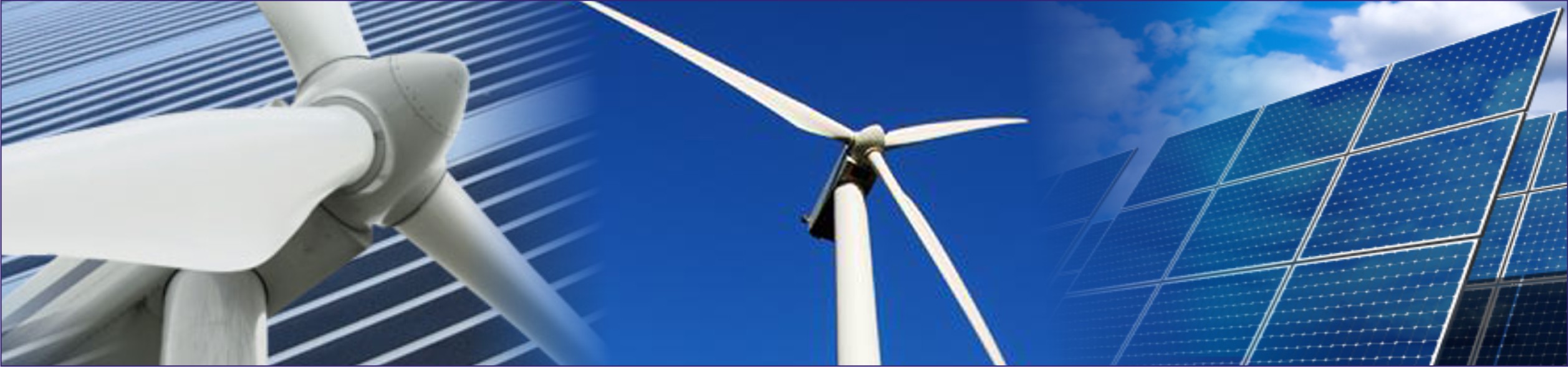
REpower Systems SE and Alerion CleanPower Spa, an Italian-based renewable energy company, signed a contract for a wind project in the South of Italy. REpower will deliver 13 3.4M104 wind turbines to San Marco in Lamis, a 44 megawatt (MW) wind farm situated north-east of Foggia. The turbines will have a rated output of 3.4 megawatts and a hub height of 80 meters each. REpower is responsible for supplying, installing and commissioning the turbines. The company will also provide service in line with a twelve years service agreement with Alerion CleanPower.
San Marco in Lamis wind farm is located close to REpower Italia’s main service center near Foggia and will be maintained directly from there. The Italian-based subsidiary of REpower Systems SE will start construction as early as the fall of 2011.
Andreas Nauen, CEO of REpower Systems SE, is pleased that REpower’s 3.XM series is well accepted on the Italian market: “This is the second contract for the 3.4M104 in Italy. It confirms the excellent market-fit of this turbine and strengthens our market presence in Italy.”
Carlo Schiapparelli, Managing Director of REpower Italia S.r.l., comments, “We are delighted to be working with Alerion again. Our first project, Ordona, with 17 REpower MM92 turbines was completed in 2007. This second project confirms that Alerion – an important client for REpower Italia with a high level of renewable energy expertise – regards us as reliable supplier.”